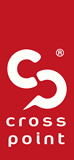
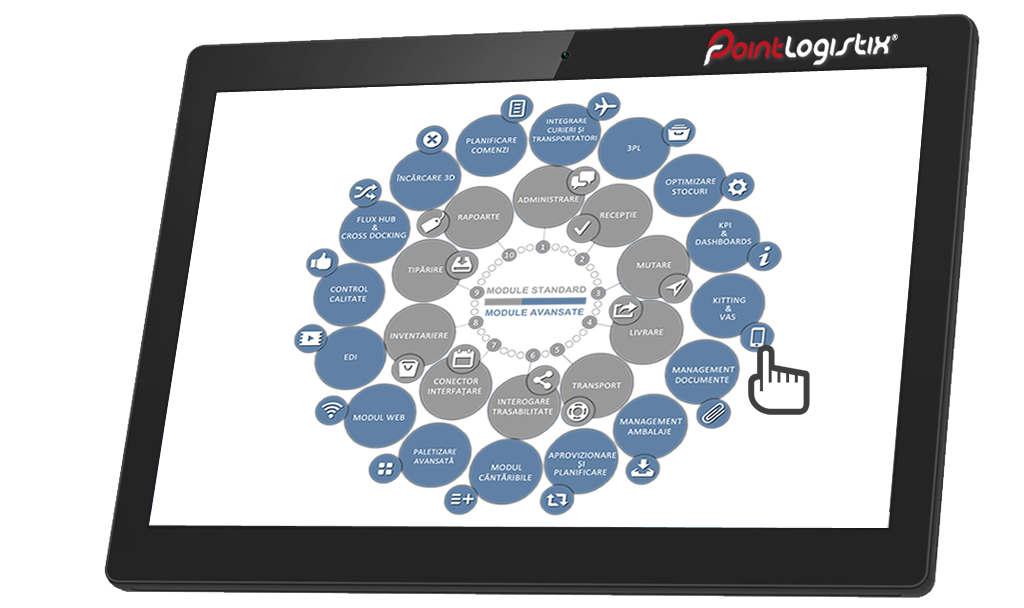
CROSSPOINT ARCHITECTURE
STANDARD MODULES
The Crosspoint suite structure is modular. The core area covers the logistic flows necessary for stock management. Crosspoint features 500 functionalities that can be enabled based on the specific activity of the client. For each type of operation (reception, put-away, replenishment, picking, consolidation, loading, etc.) there are multiple scenarios available (implemented and tested) from which the project team selects during the project review period. Of course, they can be tailored to specific requirements, but their integration into existing streams minimizes the time spent on personalizations and acceptance tests.
OPTIONAL MODULES
For companies that have a greater complexity of activity or who want to improve certain areas of logistics, the optional modules of the suite are designed to add value.
Although they are optional, some of these can be identified as critical to the project, and they are the goal of initial implementation, others are mature in use of the suite and can be activated at any time later.
Within these modules, 400 more functionalities make it possible to implement multiple scenarios.
More information
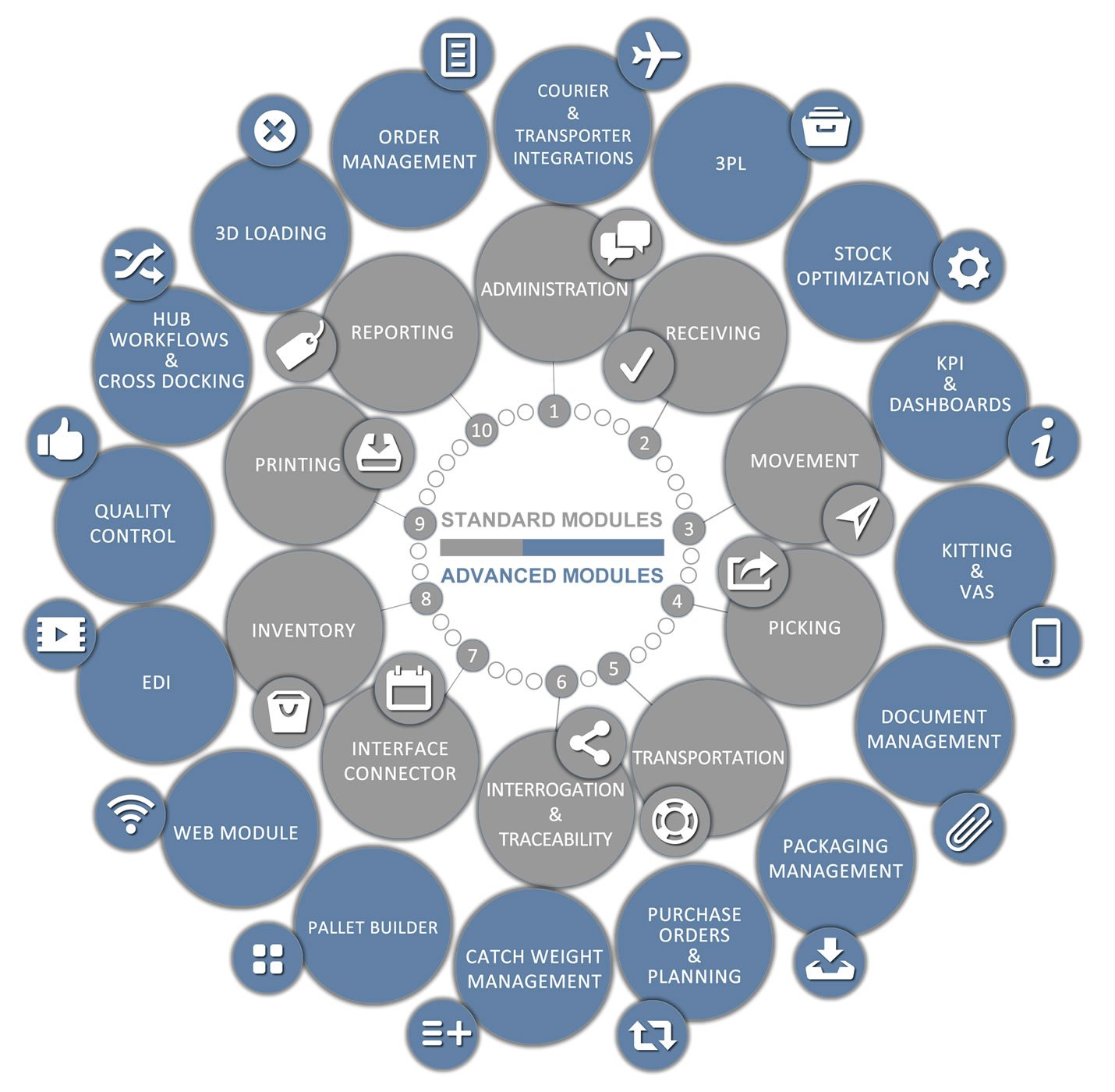
Crosspoint architecture
The Crosspoint suite is designed to automate the management of any warehouse. Terminals permanently communicate with the database over the wireless network.
The structure is modular. The core area covers the logistic flows necessary for stock management. Crosspoint features 500 functionalities that can be enabled based on the specific activity of the client.
For companies that have a greater complexity of activity or who want to improve certain areas of logistics, the optional modules of the suite are designed to add value.
Curier and Carriers Integration
For delivering courier solutions companies, AWB generation is WMS integrated functionality that allows not only label printing, but also tracking package statuses, generating non-delivery receipts, cash on delivery tracking, and billing of services by the transport partner.
For the classical transport area, tracking an order / shipping bills allows advanced cost analysis of the distributed to the freight or group of goods and customer.
Multi-courier integrations are transparent to end-users by contextually communicating with the carrier assigned to the transport command. Both AWB generated in picking and consolidation are allowed. At customer-level, multi-parcel shipping notes can be generated, which is part of the shipping load process.
The acquisition of intermediate and final statuses in courier systems is automated and integrated with other IT solutions (e-commerce, SMS, etc.).
Planning
Managing and scheduling customer orders, based on availability (warehouse, supplier stock or production capability), allows a unitary task of the Planning, Purchasing / Production, Logistics / Transport and Commercial departments and provides a clear picture of the status of these orders.
Interdepartmental requests and replanning are tracked at the approval level and are to be found in the reporting area. The WEB module can complete the flow by providing direct access to customers or suppliers.
Flow segmentation can be done from user rights. This way, order confirmation and communication with the customer acquisition department can be separated from logistic planning at the warehouse level. The loading and shipping area in the shipping segment completes traceability in this case.
The ability to access the planned inventory in the production or relocation phase is essential as the specificity approaches Just in Time.
3D loading
For warehouses with challenges from the variety of final packing (different types of pallets, boxes), the module enables automatic generation of loading scenarios. Preconditioned transport rules are taken into consideration: overload, axle weight, multiple download sequence planning, and prioritization of control lines.
The 3D solution, approved by a transport department, brings significant improvements to the level of truckload and is then transposed into the loading module used by warehouse operators.
Administration
The Administration Module allows you to define WMS-specific items (storage map, locations, storage rules, put-away, picking and replenishment) and editing information retrieved from external systems.
The warehouse can be defined at the level of physical rows, management, storage rules (assigned areas, rotation speed criteria, dedicated products, optimized picking path). Defined areas can be physical or virtual. Special cells (reception, ramps, services, delivery, docks) are delimited.
Partners may include suppliers, carriers, cargo holders, consignees and delivery addresses.
The products receive specific features in addition to those imported (if applicable): dimensions, bundles, tracking type (batch and expiration date, serial number), preferred delivery criterion (FEFO, FIFO, FMFO) temperature, manufacturer's standard), codes (unlimited codes per item, client specific codes, specific packaging methods, images).
Reporting
The Report Module contains a complete set of information including:
■ Stock (total, by area, by group of items);
■ Shelf (per item, batch or serial number);
■ Receipt, delivery, shipping and inventory history;
■ User activity and productivity;
■ Resources used (printed labels, equipment usage etc.);
■ Short-term products;
■ Warehouse occupancy rate;
■ Stock rotation;
■ Stock history;
■ Stock to date;
■ User login history;
■ Number of transactions per type and period;
■ Article traceability;
■ Pallet traceability;
■ Location traceability;
■ Batch traceability.
Printing
The Label Printing module allows tasks tagging alocated to the types of operations integrated with operator flows:
■ Reception Pallet Label issued when receiving the goods. Pallet codes or collective packaging unit codes help identify more products at a time
■ Pallet picking tag
■ Move palette tag . It results in the de-consolidation of the palletized goods.
■ Inventory Pallet Tag . It is used for physically reorganized goods in the inventory process.
■ Preprinted Labels . Where contextual printing is not required to perform operations, the "blind" labels ensure the unique serialization of created pallets.
■ Order Label
■ Article tag . Product barcodes will be the default ones provided by the manufacturer. If products do not have a barcode, they will be generated at the collector or unit packet reception level, depending on customer requirements.
■ Item Label / Customer Specific Batch
■ Location Tag . Ease work in the warehouse by labeling shelf or bulk cells. Labels contain the barcode and alphanumeric storage position code.
Back-office operators can request the regeneration of labels in case of damage.
Inventory
Back Office Inventory Module allows inventory or check orders to be created, at warehouse level, product list, or cell list (e.g., inventory at ground level etc.). Depending on the final decision, the inventory result may be closed as a check or may overwrite the stock by automatically issuing a receipt and a delivery note.
Front Office Inventory can be performed on multiple terminals simultaneously, downloading data cumulatively.
Inventory can be done in several ways:
■ successive counts;
■ simultaneous counts;
■ Cyclic inventory - it does not imply interruption of activity. The system automatically indicates the oldest non-inventory locations and generates interim postings prior to the official approval of the plus and minus results at the end of the inventory cycle.
Interfacing
To help connect with external systems (ERP, CRM, SFA, etc.), the Crosspoint Interface Connector provides standard data transfer formats (csv, txt, shared tables, sockets, or REST, asynchronous imports) ensuring that all transactions between systems are monitored.
Any transaction can be tracked through the initialization time, execution status and a reason for a denial in case of error. Transactions can be re-imported automatically or manually after resolving the source issue.
There are over 30 standard interfaces that can be enabled according to project specificity and data retrieval needs.
Currently, 35 ERP solutions have connectors already available in Crosspoint, which minimizes activation and integration time. The logic may vary depending on the type of transaction (vendor reception, return receipt, client order, transfer order).
Query and Traceability
The Back Office Query Module provides the Back Office user access to a minimum of time for any information in the system. Item code, batch, article name, warehouse, receipt, move, delivery, shipping, external document (invoice, external system order), serial number, partner code, etc. can be searched for.
The Front Office Query Module allows users to have inventory information on the field. Searches can be: item, batch, serial number, container code or location. For usability, this functionality is available contextually at all stages of the process.
The Back Office Traceability Module provides immediate tracking data for batch tracing, palet history, warehouse stock, SKU movements from reception to warehouse exit. Each operation has logged the exact duration of completion and the user assigned to.
Transport
Back Office Transport Module - Allows to create transport orders, assigned to a carrier, driver or truck, by adding multiple commands to the system. Creation criteria can go from fixed pre-configured routes or user input to zones, the system generating dimensional alerts depending on the type of truck selected. Upon completion, a packing list and shipping manifest are issued with consolidated cargo data. The module can be connected to advanced features that enable truck programming and qualitative reception, shipping costs control, across the included cargo categories, integration with partner systems. For your own fleet, Crosspoint Fleet Management ensures complete tracking of maintenance operations, documents attached to each vehicle, and cost-center traceability and road mapping.
Front Office Transport Module - When loading a car, a load order is issued on the mobile terminals. Users have to scan the loaded pallets (with loading order imposed or not) to confirm the exit from the warehouse. The module can be connected to advanced functionalityes, to visualize the exact position where each container should be placed as planned.
Delivery
Back Office Delivery Module allows record orders input to the system. Data such as: requested delivery date, client, client work point, quantity and value data, customer order number, etc. may be recorded.
Delivery Monitor is the primary tracking order status tool. The Back Office user can launch multiple work orders, according to the chosen criteria (truck / route consolidation, zone consolidation, shelf picking, customer types). Upon completion of the orders, the accompanying documents (declaration of conformity, notices etc.) can be printed and the order confirmations can be sent automatically to the external system (ERP). The order allocation can be set automatically for certain scenarios.
Front Office Delivery Module - Confirms picking at warehouse level. Each user receives the assigned tasks. The picking order takes into consideration complex algorithms of the shortest path type, pallet stability (decreasing order of weight), etc. Standard picking strategies include: picking, batch picking, wave picking, etc.
Move
The Back Office Move Module allows you to enter a move order by the Back-Office user. The purpose of the move may be to reinforce items, batches, follow specific rules.
Movements can be done between storage locations (container, pallet, box, etc.) or between stock containers (items).
Using the Inventory Optimization module allows you to automatically generate such orders based on the dynamics of the warehouse activity (put away automatically when a pallet is received, replenishment when reaching the minimum or critical level at the cell level, etc.) . The settings allow stock-level consolidation strategies at the product level through the put-away pre-picking zone separated from the storage area.
The Movement Monitor lets you monitor the status of the move orders.
The operations available through the Move Front Office module are:
■ system-directed (put-away, replenishment) at pallet or article level;
■ those made by users with sufficient permissions to:
& nbsp; & nbsp; ■ Manually move the pallets
& nbsp; & nbsp; ■ manually move items
& nbsp; & nbsp; ■ Product synergy
& nbsp; & nbsp; ■ Palette burst
& nbsp; & nbsp; ■ pallet consolidation
Receiving
The Back Office Reception Module allows you to enter scripted documents when they are not imported from an external system, and the document type does not require that it be started from the Front Office module. For return documents, links to source documents can be made.
Reception Monitor lets you track the status of your active documents. The goal may be viewing for some users and reallocating for those in the role of team leader. Assignment of tasks can be dynamic or static, with the user with the necessary rights to intervene and make momentary decisions. The status of work order evolution is in real time.
Front Office Reception accommodates over 12 common scenarios. It is usually done on mobile terminals that allow the assignment of a unique code (pallet ID) in the system for each received packing unit. Depending on the desired restrictions, the received pallets may be mixed or unique at the product type (possibly batch). Integration of value-added services, qualitative checks or put-away areas can be set at the transaction type.
STANDARD MODULES
The application structure is modular. The core area covers the logistics flows necessary for the management of any management. Includes 500 features that can be enabled based on the specific activity of the recipient.
For each type of operation (reception, put-away, replenishment, picking, consolidation, loading, etc.) there are multiple scenarios available (implemented and tested) from which the project team selects during the project review period. Of course, they can be tailored to specific requirements, but their integration into existing streams minimizes the time spent on personalizations and acceptance tests.
OPTIONAL MODULES
For companies that have a greater complexity of activity or who want to improve certain areas of logistics, the optional modules of the suite are designed to add value.
Although they are optional, some of these can be identified as critical to the project, and they are the goal of initial implementation, others are mature in use of the suite and can be activated at any time later.
Within these modules, 400 features make it possible to implement multiple scenarios.
3PL
The module allows you to manage the stock operations of multiple companies. Through the traceability offered and the activation of functionalities in the financial analysis area, it is facilitated:
■ billing of deposit services defined on the basis of service contracts;
■ billing of transport services defined on the basis of service contracts;
■ cost tracking per operation;
■ normalization of activities;
■ tracking profitability by type of operation and customer.
It is allowed to have the same article in the list of several cargo holders and repeat the same bar code to different holders. Some documents and entities managed by the system are directly linked to the holder (reception, delivery, pallet, article), others allow multi-carrier operations (move, transport, inventory, location).
Stocks optimisation
Inventory Optimization Module allows you to set multiple automatisms by which warehouse managers can impose how operators perform tasks. The system thus carries out automatic guidance in determining the put-away and replenishment storage areas dependent on different product and customer groups.
Settings can be made at the transaction type, warehouse, and group of traded items. Limit stocks (minimum, maximum) can be defined to generate refueling requests at zone or warehouse level.
It is allowed both vertical replenishment with minimum, maximum, critical criticality per dedicated location, and horizontally for buffer picking area for example.
In the case of batch products, the expiration date involves distinct rules in both the order of re-supply and the direction of receipt of the goods, allowing for a correct stock rotation and diminishing short-term expiration products.
For Bulk Areas, set criteria are created that allow for FIFO-compliant compliance after a set number of days set by article manager.
In general, the priority of the criteria is controlled by prioritization indices and by exception of users with sufficient rights.
KPI & Dashboards
Any project brings to the analysis area the main performance indicators that are wanted to be monitored as well as their accepted values.
The KPI area addresses commonly used logistics indicators as well as indicators specifically defined for the logistics or production centers in the project. Among the included indicators we mention:
■ On Time Delivery (OTD) / On Time Delivery (OTIF);
■ Inventory accuracy;
■ Resource use;
■ Delivery;
■ Average command time;
■ Stock Rotation.
The Dashboards module makes the reaction at the time of loading immediately. Resource reallocation decisions can be made in real time, based on the planned and estimated time of open operations in the system. Administrators have access to complete definition of dashboards, their content and limit parameters.
Kitting & VAS
Activities with increased complexity including the Bill of Material (BOM) can be traced and are natively integrated into the traceability offered by the Crosspoint solution. In the service area they are priced according to the grids agreed with the final customers. The system automatically generates output document on Output and Output Document for Components. To ensure the need for stock replenishment in the service area packaging is available taking into account commercial conditions customers.
Variable component recipes are permitted to solve specific high complexity streams. For certain components, it is possible to define prescriptionable interchangeable items.
It is permissible to define packaging that is consumed at the prescription level and the component operations as a regular and effective effort. For stock-level, wrap-up, or transport-level items, the labels set by system administrators can automatically be issued.
Document Management
For better tracking of document traceability, both those issued from solution modules and external documents (notice, invoice, CMR, upload and download images, quality and warranty certificates, etc.) can be attached.
The module allows for complete tracking of the route from issue to archiving.
In the case of deliveries to the Key Account networks for FMCG implementations, the flow of endorsement, final document confirmation, receipt reference, billing based on accepted delivery quantities are integrated into the document flow.
For the service and e-commerce implementations to which delivery documents are automatically generated by customer systems, the module proves useful to attach the documents received with WMS transactions by facilitating the flow of print notice, invoice, AWB , etc.
Packaging Management
Items that come with returnable packaging can be easily tracked by activating this module. Both in the supplier replenishment area and customer custody monitoring, it is flexible to provide real-time information on the stock of this type.
For companies that include production flow, a clear differentiation of inventories can be achieved on each management and warehouse.
Representation of the stock in custody is a double one representing the responsibility of the carrier / recovery driver and the customer custody at the same time. Warranty reports can be issued or entered. The percentage of recovery per customer as well as the management of special packaging (eg CHEP pallets for which management is required but recovery does not come within the company's responsibility).
The use of the module allows for the correct estimation of the volume of packaging required and the generation of re-supply proposals from the supplier.
Inventory is possible on both its own management level and the custody stock at the client workstation level.
Supply and Planning
Through extended module functionality, sales forecast, stock analysis, CMZ (daily average order) and VMZ (daily average sales) allow issuing and tracking orders to the vendor. The attached report set measures both the performance of the vendor and the impact of OOS (out of stock) on the supply segment.
The system analyzes customized rules based on vendor and product range rules for outgoing transaction rules as well as parameters on that vendor per item. A Purchase Order proposal is issued that can be modified by the Purchasing department. The application is issued with a single series to the supplier and can be re-imported after approval with the final quantities approved by the supplier.
Input documents are related to supply commands, as appropriate, using the presence of the Document / Item / Palette reference number, or by user-approved automatic distribution based on FIFO consumption of open supply commands in the system.
The weighing module
To handle variable weight products, the module comes with a number of functionalities that make it possible to clearly distinguish the actual stock and stock management differences of these products.
In most cases, the implementation is done with the integration of the solution with the weighing systems in the warehouses where it is implemented to allow direct capture of the weight on the mobile terminals. Also return management management can be easily implemented at the same time.
The correct handling of these types of articles is based on a rigorous administration of primary and secondary packaging that allows automatic determination of the tare and the correct determination of the gross weight of the stock containers. Flow may involve activating a mandatory pallet check after the picking process is complete.
If some packages have variable weight over established margins (eg pallets), it is possible to pre-order those with unique internal codes that have the actual weight attached.
Advanced Paletting
For articles with a well-defined palette layer definition, the module offers automated blending of mixed blades based on defined overlaying rules. Operators in the warehouse have the task of physically accomplishing the tasks generated by the system.
WEB module
For partners who need to access reports and management command modules without using the Back-Office component, this is the easiest way to access WMS.
Starting from these basic functionalities, the information or fluxes defined are adapted to the project requirements.
Any of the supply chain areas may be allocated to a segment where external users of the warehouse interact with WMS Crosspoint. Some implemented scenarios include:
■ Possible provider of item nomenclature upload, stock availability and pricing policies, order tracking and similar market placement;
■ Delivery feedback monitoring system by confirming containers, packages and goods following destination reception;
■ 3PL warehouse management without solution involving scanning;
■ Introduction Transport commands to the responsible department.
EDI
In the flow of communications to existing suppliers, customers and solutions, the EDI capabilities of the solution allow easy integration of the various transactions that are wanted to be pursued. Different industry-specific standards (EDI-FACT, ODETTE, AS2) are implemented.
Many of the projects involve not necessarily implementing standards, such as connecting to the required WMS solutions. The ability to cover various integration technologies and integrate them quickly (csv, txt, shared tables, sockets, SOAP or REST Web services, asynchronous imports) is an important asset of the Crosspoint suite. The new interfaces are transformed into the standard ones of the suite, providing essential stability and minimal testing time.
The most commonly integrated systems include: ERP, IT vendor systems (in acquisition area and master data), SFA, CRM, TMS, IT system carriers / couriers, IT customer systems (in the dispatch area, automatic import orders and receipt confirmation custom), BI, e-commerce.
Quality control
For companies where Quality Departments work closely with inventory stocks (production companies), the Crosspoint solution includes facilities that allow the collaborative work of Logistics and Quality teams:
■ control plans;
■ frequency of validation of operations;
■ unblocking batch of critical materials and finished products.
At batch, pallet, or entry level, qualitative reasons can be set for delivery restrictions, possible relocation tasks, or qualitative inspections. The complete traceability of these operations allows for accurate tracking of incidents and activity in the Quality area.
Quality bulletins, warranty certificates, or other specific quality documentation and documentation can be tracked.
Flux HUB & Cross Docking
For companies with multi-storey structures, trace of a prepared order in a source warehouse can be traced to the final hub from which it is delivered to the customer.
Any parcel / pallet can also be monitored without its stock being necessarily known.
Functions of this type are also useful for implementing pick-up points in the e-commerce area.
Proper tracking has multiple benefits:
■ correlation of physical traceability irrespective of the ERP flow (customer billing deposit may be the source);
■ Receiving cross-docking specific flow receipt at interim warehouse reception;
■ flow tracking and possible return of packaging;
■ document management at flow level;
■ Confirm correct charging to the correct destination at any step in the stream.
%
Operator efficiency
%
Process performance
%
Stock accuracy
%
Services rendered
CROSSPOINT FEATURES
■ Map configurable at the level of rows, floors, columns;
■ Bulk or island locations;
■ Multiple cell states and storage type (picking, pallet, etc);
■ User-configurable features of allocated groups;
■ Volumetric settings, storage temperature and special conditions;
■ Put-away, picking and access-enabled settings;
■ Pick up order;
■ Replenishment settings;
■ Shared inventory management allocation.
■ Settlement traceability set (lot, serial number, entry document);
■ Default download type (FIFO, FEFO, FMFO);
■ Item configurable attributes;
■ Multiple barcodes and specific partner codes (vendor or payee);
■ Multiple alternative units with the possibility of assigning the bar code list per each;
■ Kit items (Bill Of Material);
■ Multiple configurable batch attributes;
■ Multiple palette attributes (vendor SSCC, manufacturer code, supply number);
■ Dimensional attributes (net weight, gross weight, volumetry);
■ Variable number of classifications.
■ Possibility of restricting or permitting certain locations as the merchandise of several holders to be stored at the same time;
■ Put-away, replenishment, cargo-dependent picking strategy;
■ Integrate contract management for service provision;
■ Billing mode auto-invoicing integration of 3PL type services;
■ Packaging stock management on each freight owner;
■ Inventory by customer or subgroup of cargo;
■ Notifications, labels and custom document templates per freight owner;
■ Multi-ERP integration.
■ Logging of each operation performed on a device-based and application-based system;
■ Possibility to access location inventory information at any historical time;
■ Warehouse load analysis and number of operations at any time in the past;
■ Upward or downward traceability;
■ Specific quality documents and determinations that can be integrated through the Document Management area;
■ Vendor Batch Tracking per Entry and Stock Container Received.
■ Pick by Order ■ Wave Picking ■ Batch Picking ■ Zone Picking ■ First Match First Out ■ Cross Docking ■ Replenishment 1/2 steps ■ Assign multiple resources to the task ■ Dynamic prioritization and on demand ■ Restrictions on equipment and users |
■ RF ■ Pick-to-Light ■ Put-to-Light ■ Voice Picking ■ Integration of Conveyor sorting ■ AS / RS ■ Integration of weighing equipment ■ Integration of marking equipment ■ RFID tags / tags ■ Integration of production lines |
■ Definition of integrated weighing equipment;
■ Lifting equipment;
■ Item allocation, zone to access resource type;
■ Possibility of blocking equipment or assigning to task;
■ Definition of data capture equipment and user login monitoring;
■ Bluetooth integration capability;
■ Equipment grade reports;
■ Historical usage analysis and sizing scenarios increasing activity with existing resources.