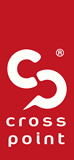
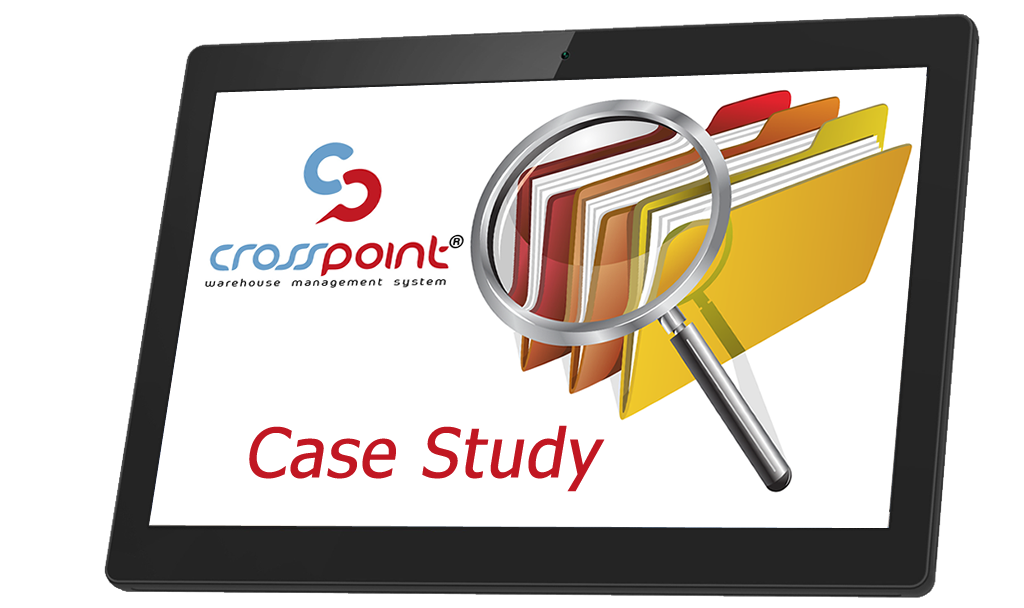
CROSSPOINT IMPLEMENTATION – CASE STUDY
About the Company
The Fashion Days story began in 2009, with the mission of giving access to exclusive brands designed to contribute to a positive change in look and style. In the years to come, the company has evolved and has become a complete product: an online shop with an impressive variety of products and brands, accessible anywhere and anytime.
Now it is the fashionable destination of Romania, Bulgaria and Hungary. It offers hundreds of thousands of products from an impressive variety of brands.
ELA Award
In the 2015 edition of the European Gold Medal in Logistics & Supply Chain, the Project of the Year category, Fashion Days took third place with the “Logistics and Operations with Style“, the competition being represented by projects from all European countries, members of ELA.
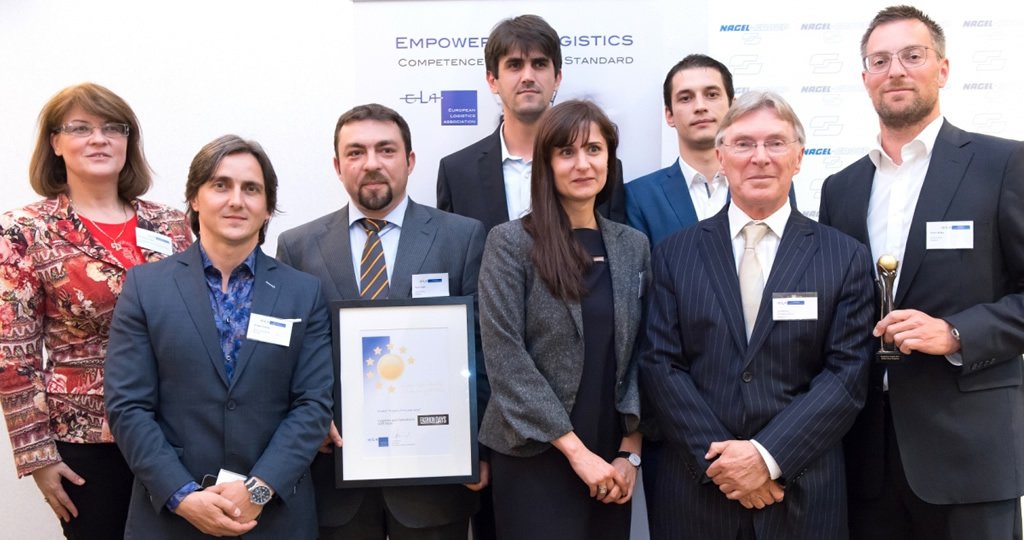
Some of the project challenges
- The high number of commands during the go-live;
- High number of transactions per second;
- Concurrent implementation of WMS and conveyor solutions;
- Constant business changes (volumes, number of deposits, peak periods);
- Integration of over 200 new users into the system;
- Variety of rules brought by concurrent delivery to 10 different countries
- Very short migration time
- IT teams geographically separated at infrastructure level, monitoring, business flows;
- Initial expansion from 1 to 3 warehouses, then consolidation of operations through a migration that had to allow concurrently existing flows set and those adapted to the new logistics center;
- High volume transactions interfaced with external systems
- Implement billing and printable policies at WMS solution level
- Various types of merchandise with distinct logistic behavior
Solution
Go-live in the Fashion Days warehouse was held on May 11, 2013, four months after the start of the project.
Subsequent expansion ranged from the implementation of 2 more warehouses to migration to a new logistics center.
The positive results were immediate. Stock Accuracy exceeded 99.998%, and volume duplications could be made without significant changes in the chart of the chart.
Crosspoint transformation into the central IT system used in logistics was allowed by interfaces between IT systems that allowed more than 100,000 daily transactions exchanged between systems.
From a functional point of view, including streams such as RMA and cycle count allowed both performance increase and greater transparency to other departments.
The decision to serialize the exceptions identified at the reception and to include in the system the traceability of the refused returns made Crosspoint to monitor the real situation on the ground beyond the bookkeeping stocks maintained at the level of financial accounting solutions.
Crosspoint WMS
Testimonial Paul COPIL
Chief Operations Officer,
Fashion Days:
- WMS deployment motivation
- post-implementation results
- direct and indirect benefits
- return on investment
- relationship with the implementation team
- Feedback on using Crosspoint
Initially implemented features:
Reception
Put Away
Conveyor Integration
Courier integration
Billing
Consolidation & Transport
Wave picking
Further implemented features:
Periodic inventory
RMA (Return merchandise authorization)
Stock in consignment
Weighing parcels
Manual batch picking
Conveyor separation of single line flow
Separate samples at the receiving
Bulk stocks delivery
Dashboard
Transfer to external deposits
BI integration (Business Intelligence)
Request details!
-
Do you want to know more about the operations in your own warehouses to optimize them and reduce costs?
POST-IMPLEMENTATION RESULTS
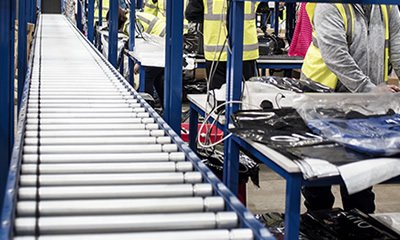
Automation
A new fully automated conveyor has been installed and synchronized with Crosspoint WMS. By using an internal bar code system and redundant scanning, the speed was improved by 700% while the FTE was reduced by 65% and the error rate dropped to a subunit.
1.500
commands/hour
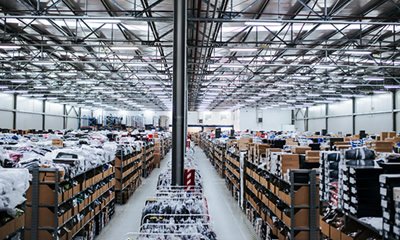
Intelligent storage
By implementing the used chaotic storage system, reception and picking times were improved by 400%.
A square meter of shelf can contain up to 500 products and the entire stock is now available in real time.
1.2 MIL
stock items
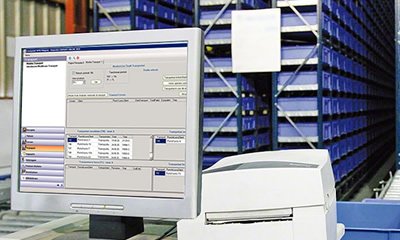
Control
Each stage of the process is fully monitored and controlled.
Several systems ensure the transparency and monitoring of processes, financial operations and customer feedback.
BI Platform stores all data for reporting.
10,000
transactions/hour
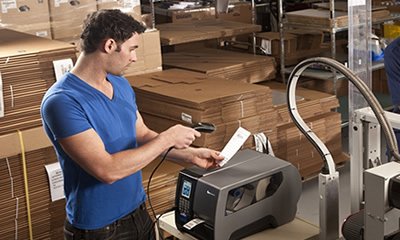
Transform
The operational process has been completely redesigned and adapted to the shift from flash sales to retail.
Implementing Crosspoint WMS ensures inventory control and complete traceability from delivery to customer returns.
0.01%
processing errors
Crosspoint
High Reliability Solution with Low Operating Costs
Prior to implementing the automation, 210 people in three shifts worked with the Distribution Center, with 70 people per shift, reaching a maximum of 200 orders/hour with a 30 minute average processing time per order.
Currently, there are only two shifts, with 35 people per shift, and the processing capacity has increased to 1,500 orders per hour, with an average processing time of less than 5 minutes per order. In addition, even if the processing speed has increased enormously, errors have fallen from 7% to less than 0.01%.
In the case of salespeaks, the system proves its flexibility, allowing an increase in processing capacity by installing additional packaging stations or expanding to the third stage.
The WMS can easily be upgraded and expanded due to the modular construction. Moreover, extra staff do not require special training – everything can be learned in up to 4 hours.
The system also provides full traceability of the product, indicating what the operator did, the quality check, packing or shipping, who the driver was, what the package was transported, etc.
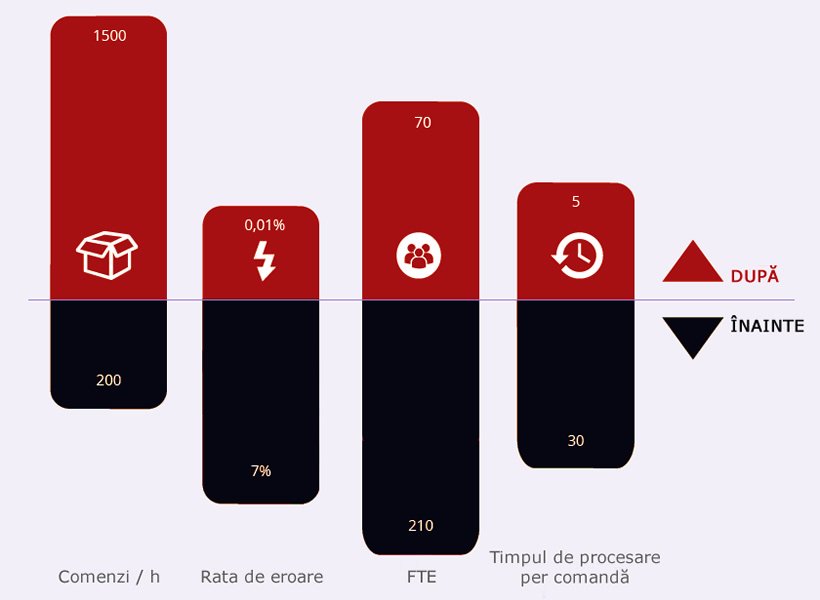
Case studies
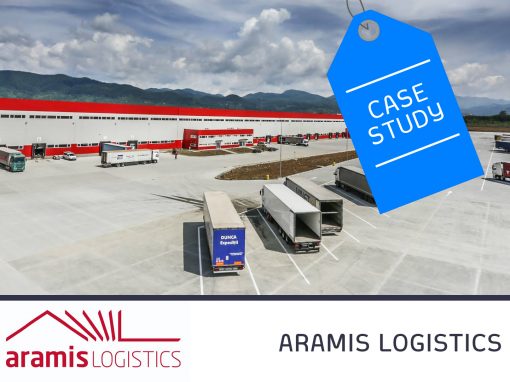
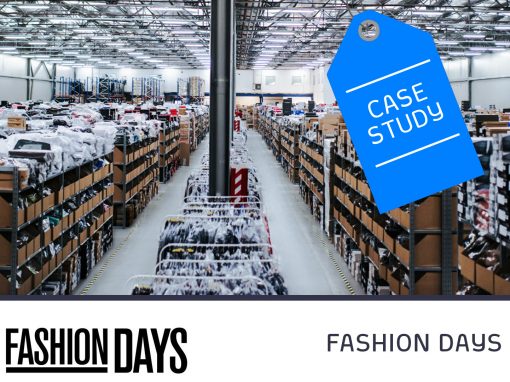
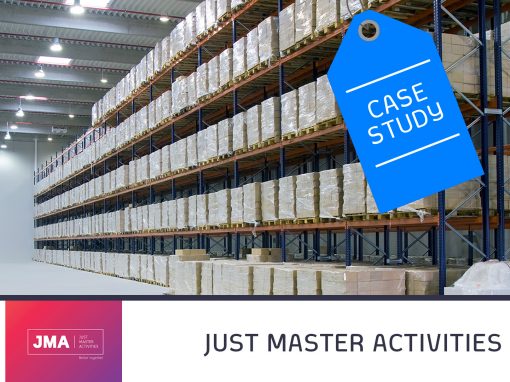
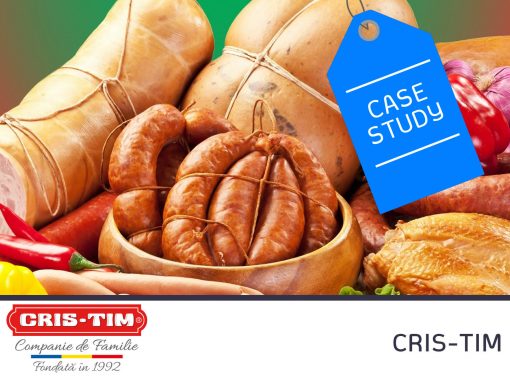
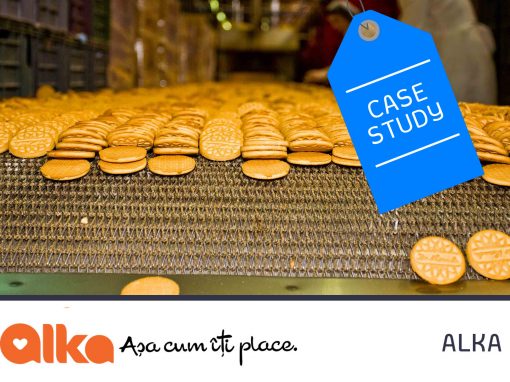