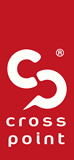
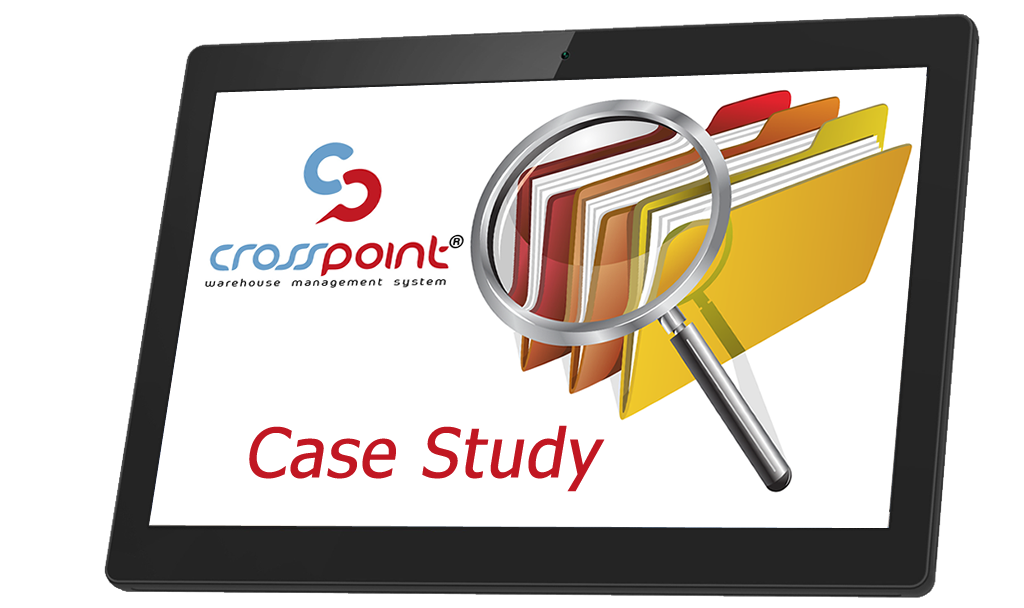
CROSSPOINT IMPLEMENTATION – CASE STUDY
About Company
Alka is one of the leaders of the Romanian market in most of the categories in which they are present, but they like to believe that it is not the sales figures that represent them but the things that stand behind them : the taste, the state of well-being and the many pleasant surprises it offers to consumers.
I place my soul and passion in everything I do and seek to inspire this state of well-being everywhere, offering for over two decades the highest quality products, along with the care for every detail.
Some of the project challenges
Reduced space (available at the central repository at the time of the initial go-live) compared to the large amount of items to manage;
Existence of goods in custody to third parties;
Diversity of sales channels served:
- Platform
- KA Magazine
- Indirect Distribution
- Direct Distribution
- Regional Deposits
- Export
Management of own and purchased items from suppliers;
The limitations imposed by the existing ERP solution;
The short time allocated to initial implementation;
Strong activity in warehouses (24/6), without the possibility of an interruption in WMS initialization.
Solution
Implementation of WMS Crosspoint within the Alka group began at the end of 2009 by analyzing the remodeling of logistics processes in the new WMS solution and in the already used ERP solution.
Go-live in the central warehouse in Bucharest took place on March 1, 2010. Over the next few months, the solution was extended to 9 other regional warehouses. The increased accuracy required in the traceability of raw materials required that Alka Co’s main warehouse be implemented in the same year.
The emphasis was on achieving complete traceability, while improving the speed of order preparation.
The migration to the new Logistics Center in Mogosoaia in 2016 forced the activation of new functionalities needed to adapt to new flows. Crosspoint’s flexibility allowed simultaneous parallel flow operations of the two deposits (old and new) during the move.
In the Inventory Optimization area (palette replenishment, article, product-specific put-away and destination-export client – temperature, volume and weight-dependent storage rules) advanced algorithms have been enabled, enabling the activity to be automated yet from the first transfer day.
Initially implemented features:
Individual order preparation
Individual order preparation
Kitting
Integrate with factory production delivery mode
SSCC integrated external suppliers
Stock optimization: Advanced putaway and replenishment criteria
Features later implemented:
KPI and Norming activities
Packaging management
Once the pallet management service was outsourced, it was necessary to adapt the working mode to the supplier’s requirements. It was necessary to keep a strict record of the packaging accompanying documents.
Multi-holders
Crosspoint integration - BI
Traceability of Raw Materials and Supply
Request details!
-
Do you want to know more about the operations in your own warehouses to optimize them and reduce costs?
- Stock accuracy 100%
- Serving in logistics 97%
- Employee efficiency 90%
- Quality control 98%
Very good outcomes
Case studies
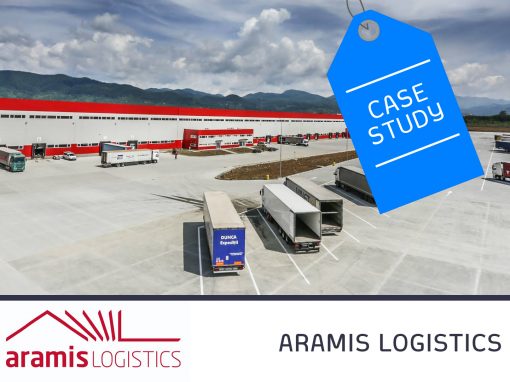
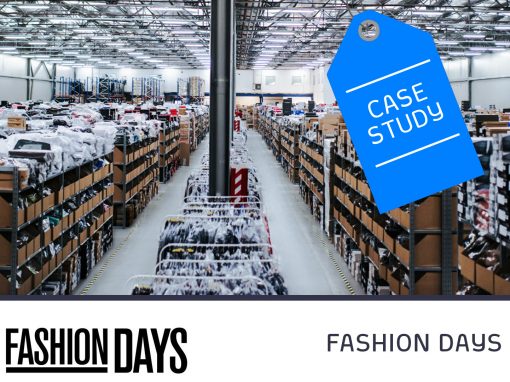
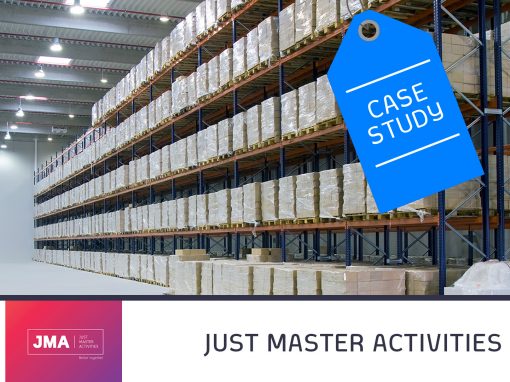
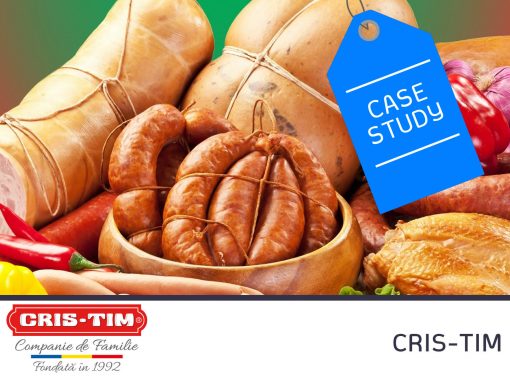
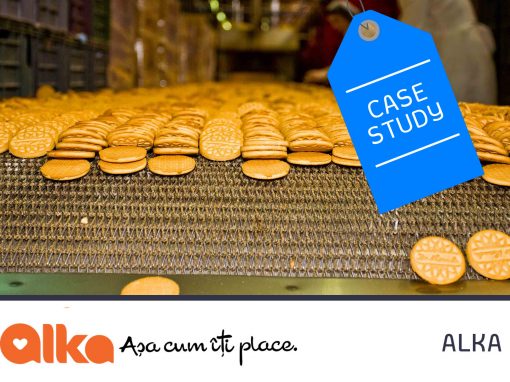