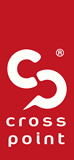
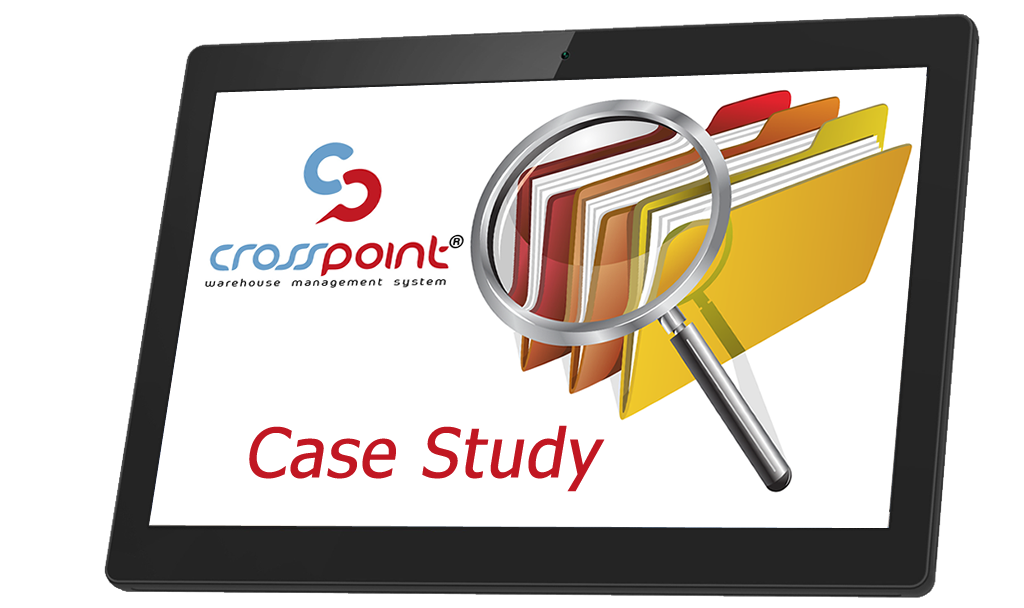
CROSSPOINT IMPLEMENTATION – CASE STUDY
About the Company
Cris-Tim is one of the best-known companies in the Romanian sausage market, based on some important values: care for people, responsibility, innovation, tradition and quality . We offer a diverse range of safe and fresh food products. The main objective of all Cris-Tim points is to respect quality, product safety and environmental protection. That’s why getting quality certificates is the confirmation of meeting the highest standards.
Some of the project challenges
Large number of items of variable weight;
Diversity of the types of managed items (sausage, dairy, ready-meal);
Diversity of sales channels served:
- Platform
- Export
- KA Magazine
- Direct Distribution
- Regional Deposits
- Own Stores
- Cash and Carry Deposits
The logistics structure in continuous transformation given by the relocation of the logistics center from Mogosoaia to Filipesti;
Increasing volumes;
Changes in warehouse layout;
Strong activity in warehouses (24/6), without the possibility of an interruption in WMS initialization.
Solution
The decision to implement the Crosspoint solution within the Cris-Tim group came as a result of the requirement to unify and optimize the activities in the logistics area.
The project started in 2014 by implementing the WMS component within the central forest depot. Enlargement immediately followed the inclusion of the 6 regional deposits. Later, the Mogoşoaia Regional Headquarters was implemented, allowing for the unification of the entire logistics flow at the company level.
The related activity of other departments with a direct logistical impact such as the Auto Department, through Crosspoint Fleet Management, the Crosspoint Purchasing and Planning Purchasing department, have been brought together at the level of the Crosspoint suite implemented solutions.
Active tracking of performance metrics has led to periodic process optimization at logistics level. The implementation of advanced data capture technologies has led to better results of the Logistics department. All warehouse-level activities have been normalized and team and individual performance can be historically compared and analyzed.
Crosspoint WMS
Testimonial Radu TIMIŞ
president,
Cris-Tim Group
- WMS deployment motivation
- post-implementation results
- direct and indirect benefits
- return on investment
- relationship with the implementation team
- Feedback on using Crosspoint
WMS implementation
Logistics Manager, Grup Cris-Tim
WMS implementation
Chief of warehouse Filipeşti, Cris-Tim
WMS implementation
WMS Administrator, Grup Cris-Tim
Features of the suite initially implemented:
- Traceability at batch level and expiration date
- Reception based on TCP integration with floor scales.
- Multiple reception scenarios by type: delivery from production, external group suppliers, transfer between locations.
- Put-away palette to target storage based on system-managed rules
- Palette and shuttle replenishment for automatic pick-up refueling proposal
- Catch Weight Management for variable weight items management
- Order picking to manage volume controls;
- Wave Picking for small but large-scale commands
- Value Added Services for orders for platforms that require specific tagging and batching
- Pallet verification flow to allow uploads
- Kitting for promotional packages;
- Integrating with scales for automatic weight picking from picking scales, flooring for verification purposes and integrated into machines;
- Flux HUB has enabled the traceability of prepaid orders in a central warehouse with cross-docking through one or more regional locations to the final customer.
- Reports and KPI
- Transport to track the traceability of the uploads and associated costs.
- Integrated IT solutions (approximately 40 active interfaces): ERP, MRP, BI, Route Optimization, SFA, GPS;
- Automatic system administrator alerts and automated reports per department
- Accumulated document printing, generating multi-command cumulative billing.
Features of the suite later implemented:
POD
Return module
The Supply and Planning Module
The Activities Standard Module
Monitoring Dashboard
Fleet Management
Packaging Management
Request details!
-
Do you want to know more about the operations in your own warehouses to optimize them and reduce costs?
- Stock accuracy 99,95%
- Accuracy of deliveries 99,83%
- Increase packaging stock accuracy 70%
- Traceability 100%
- Paperless Logistics Processes 100%
- Fast return of investment (12 months) 100%
- Inventory time 30%
Very good results
Case studies
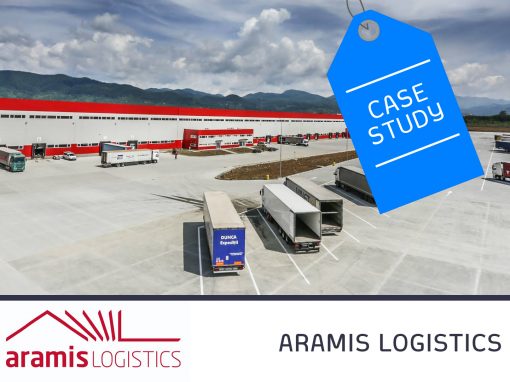
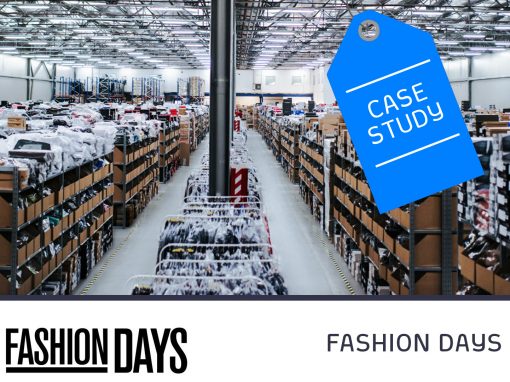
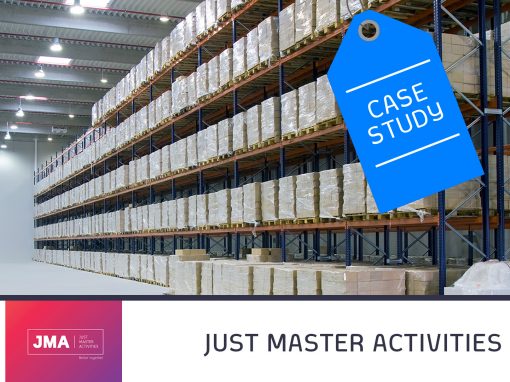
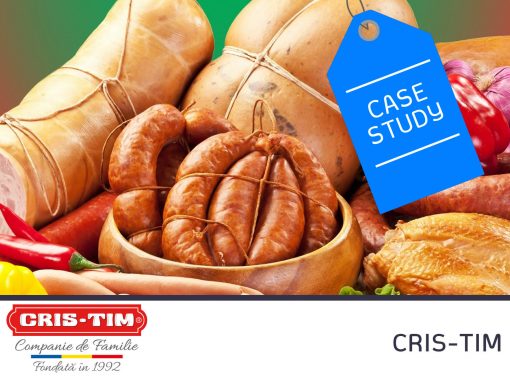
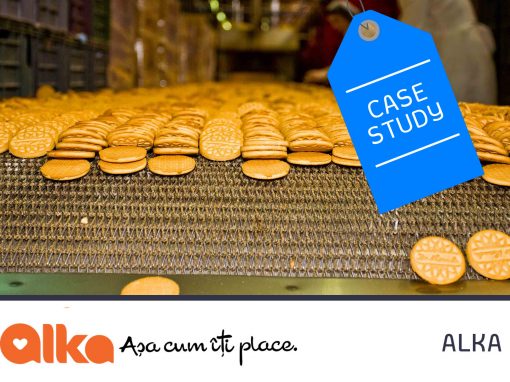